Where Your Flight Instructor and Fellow Pilots Got it Wrong.
With a decade of flying under my belt, it took nearly eight years to uncover a shocking revelation. The instructions I had absorbed from manuals, my flight instructor, and other pilots about leaning my aircraft engine were fundamentally flawed. Not intentionally misleading, but nonetheless wrong.
The root of the misinformation lies within the data we’ve adhered to for decades, teachings echoing from the era when Continental Motors and Lycoming first engineered their engines. This information is a relic from the ’40s and ’50s. Although these outdated practices should have been revised long ago, they were not.
Despite the advancements in automobile and modern aircraft engines like the Rotax 9xx iS series and the fact that these engines operate lean-of-peak whenever not operated at maximum power settings, pilots consistently operate rich-of-peak. Is it fear, misinformation, or the incorrect teachings from initial pilot training that perpetuate this practice?
Why a Different Approach Is Better
Our partner, General Aviation Modifications, Inc. (GAMI), has conducted thousands of tests on customised engine stands. This data-driven approach seeks to debunk the myths surrounding the practice of aircraft engine leaning.
GAMI has installed pressure sensors on spark plugs to measure the internal pressure in each cylinder during operation. The data collected revealed that the commonly proposed leaning technique was the worst possible practice. Original manuals suggest operating the aircraft engine between peak exhaust gas temperature (EGT) and 50°F rich-of-peak (ROP) for optimal economy. For best power, they recommend between 50°F and 125°F ROP.
These guidelines turned out to be highly misleading. The suggested EGT range for best economy is the area where the internal cylinder pressure peaks, placing immense strain on the engine and its components. Operating in this range is the most detrimental for your engine’s longevity.
While some manuals have updated this information, others haven’t. More alarmingly, most operators have yet to adopt the “new” standard. Although we lack an internal cylinder pressure gauge in the cockpit, the cylinder head temperature serves as a decent approximation.
Remember, the cylinder head temperature is the closest approximation to internal cylinder pressure available to us in the cockpit.
Why Correct Leaning Matters: Longevity, Reliability, and Cost Efficiency
An informed pilot prioritises engine longevity, reliability, and cost efficiency. Operating with an incorrect fuel mixture wastes valuable resources like fuel and engine parts. It can also lead to issues like fouled spark plugs and lead deposits, causing sticky valves and other complications.
Proper operation of your aircraft engine not only reduces fuel consumption but also protects your engine from excessive wear and tear. The result is enhanced operational reliability and fewer headaches from fouled plugs or sticky valves.
The Data Speaks Volumes
Let’s take a closer look at the data. Lycoming has updated their Operator’s Manual to include the following chart. It presents the exhaust gas temperature, cylinder head temperature, power, and specific fuel consumption for a specific model, at constant RPM and Manifold Pressure.
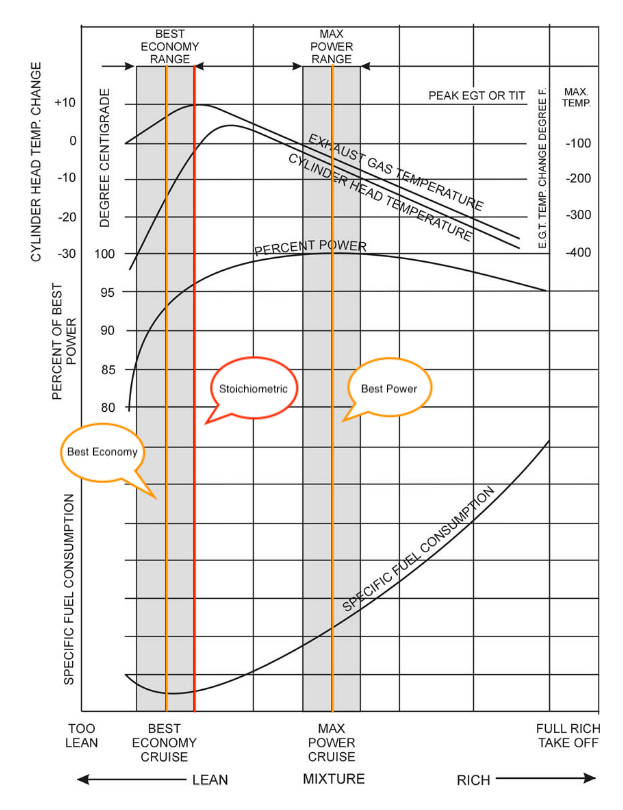
The chart provides a range for the best economy and power, but does not indicate the stoichiometric ratio clearly. We’ve added red and orange lines to identify these three points of interest.
Let’s delve deeper into the chart, as it unravels some fascinating facts. Firstly, it illustrates that the EGT peaks at the stoichiometric ratio, while the cylinder head temperature (CHT) hits its zenith at approximately 30°F – 30°F ROP. This point marks the highest internal cylinder pressure and, ironically, is often mistaken as the ideal mixture setting for optimal economy by many pilots.
Secondly, the chart reveals that the slope of the CHT is steeper on the lean side of the peak (LOP) compared to the rich side. This finding implies that a small reduction in fuel can lead to a significant decrease in the CHT (and hence, the internal cylinder pressure) on the lean side. Contrarily, a larger quantity of fuel is necessary to achieve a comparable CHT reduction on the ROP side.
The chart, therefore, emphasises the inefficiency of operating ROP during cruise flight. The speed difference between operating at 100°F ROP and 50°F LOP is a mere 6.5%, yet operating LOP reduces fuel consumption by a substantial 40%. Moreover, it’s less taxing on your engine and its components.
These insights underline the importance of understanding your engine’s performance data and using it to make informed decisions, contributing to efficient operations and the longevity of your aircraft’s engine.
Unveiling the Red Box: An Area to Avoid
Either you can operate rich-of-peak for best power (75°F – 100°F ROP), or you can operate lean-of-peak for best economy (30°F – 70°F LOP). The critical aspect to remember is avoiding the area between these points, particularly at higher power settings (above 70%). We refer to this area as the “Red Box.” The maximum CHT & ICP (Internal Cylinder Pressure) falls within the 40°F – 50°F ROP range.
We’d like to highlight two engine parameters in this context:
- EGT: The absolute EGT value indicated on the gauges is irrelevant. We only consider EGT as a limitation with turbocharged engines when indicating EGT as Turbine Inlet Temperature (TIT) for turbine protection. Aircraft engine manufacturers don’t even publish an EGT limitation, except for TIT.
- CHT: This is a key metric we observe religiously, as it affects our engine’s longevity. Aluminium alloy cylinder heads loose half their strength at 400°F and 75% of their strength at 500°F. CHT also indicates the internal stress imposed on engine components.
Both Continental Motors and Lycoming have stated CHT limits of 460°F and 500°F respectively, but these limits are only for emergencies. It’s essential to operate both Continental Motors and Lycoming engines below these limits consistently. We propose the following limits as a guidance:
Continental Motors
Maximum CHT: 400°F
Optimal CHT: 330°F – 380°F
Lycoming
Maximum CHT: 420°F
Optimal CHT: 350°F – 400°F
To better illustrate the area to be avoided, we employ the concept of the red box. We’re using the same chart as before from Lycoming to exemplify this (see below). While we don’t know the power setting or absolute values for this specific graph, it helps us communicate the intent. Suppose the change in the CHT (indicated on the left side) is 420°F at 0° deviation. Hence, we aim to avoid the area above 420°F and utilise a red box to denote the mixture settings corresponding to these particular cylinder head temperatures. For this power setting, both mixture settings – best economy (LOP) and best power (ROP) can be used. For a more conservative approach, we suggest a CHT limitation of 400°F (Lycoming), indicated by an orange box. More fuel is required to keep the CHT within the rich-of-peak (ROP) limits. Nevertheless, we can still employ a best economy (LOP) mixture strategy by leaning more.
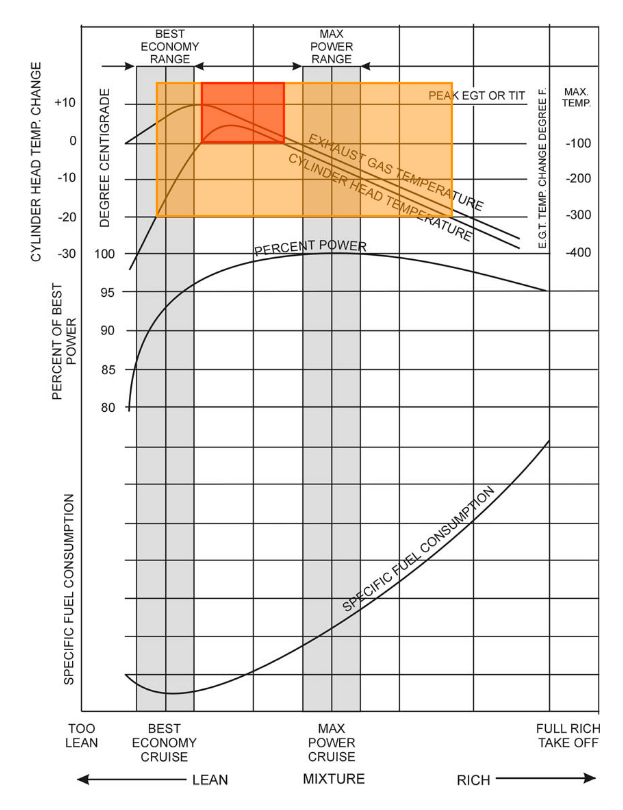
Guidelines for Leaning Your Aircraft Engine
Typically, we advise operating an aircraft engine within 75°F – 100°F ROP for optimal power and 30°F – 70°F LOP for best fuel economy, keeping in mind the CHT limitations (Red Box). For a naturally aspirated engine, the following mixture settings might be suitable:
Engine Start (Cold Engine) and Take-Off Below 3000 ft Density Altitude - Full Rich
Initiate the engine start (cold engine) and perform take-off below 3000 ft density altitude with the mixture control in the fully rich position. This protocol ensures sufficient cooling and detonation protection for take-off.
Ground, Taxi and Run-Up - Maximum RPM
While on the ground, taxiing, or running up, aggressively lean for maximum RPM.
Take-Off Above 3000 ft Density Altitude - Maximum RPM/EGT for Sea-Level Operation
When taking off above a 3000 ft density altitude, adjust the mixture for maximum RPM (fixed-pitch propeller) or equivalent EGT as observed during a sea-level take-off (constant-speed propeller).
Cruise Climb - Constant EGT
For the cruise climb, we advise reducing RPM (keep the throttle open), staying ROP, and leaning for a constant EGT.
Cruise - Choose Between ROP or LOP Operation
Now, the operation depends on your preference: either optimal power (ROP) for speed or optimal fuel economy (LOP) for distance.
- For best power (ROP): If speed is your aim, lean towards the best power mixture without exceeding the target CHT.
- For best economy (LOP): If your aim is distance, lean until the engine starts running roughly – Pull the mixture rapidly to avoid the red box. This is likely LOP for most engines, although it may be near peak EGT for carbureted engines.
Constant Monitoring of CHT and TIT
Regardless of whether you operate ROP or LOP, always monitor the cylinder head temperature (CHT) and the turbine inlet temperature (TIT). Do not let these temperatures exceed the recommended limits. If the CHT rises above the target, lean more if LOP and enrich more if ROP.
Descent - Constant EGT
During the descent, enrich as needed to maintain a constant EGT.
Landing Approach
We advise against going full rich for landing. Instead, maintain a constant EGT during the descent until landing, but ensure you’re ready to go full rich in case of a go-around.
Preparing to Master Your Aircraft Engine Leaning
To operate your aircraft engine optimally, it’s vital to acquire knowledge, ensure a balanced air-to-fuel ratio across all cylinders, and ideally, employ an engine monitoring unit.
Knowledge
Educate yourself about proficient leaning techniques and familiarise yourself with your aircraft’s specific temperature ranges and limitations. This information is essential to fine-tune your leaning skills.
GAMIjector®
A balanced air-to-fuel ratio in all cylinders is the cornerstone of effective engine leaning. This balance eliminates the onset of roughness and flame-outs and ensures all cylinders operate on the same side of peak EGT. In an unbalanced scenario, you might find one cylinder flaming out due to a lean mixture, another experiencing peak internal cylinder pressure, while yet another one operates full rich. If you’re dealing with a carbureted engine, you have limited control over this balance. However, with a fuel-injected engine, you can easily and affordably balance your air-to-fuel ratio using tools like GAMIjector® fuel injectors.
Engine Monitor Unit
While not a mandatory requirement, an engine monitoring unit greatly facilitates the leaning process. At the very least, you should have a CHT probe or indicator for each cylinder. We generally encourage installing a comprehensive engine monitor unit as early as possible, given its significant advantages for engine condition monitoring and troubleshooting.
Conclusion
Aircraft engine leaning comes with knowledge, experience, and the right equipment. As we’ve seen, the instructions of the past might not fit the technological advancements of today. We need to adapt to these changes and make the most out of the opportunities they present.
Practical Implications
The right leaning techniques impact every flight phase, optimising power, economy, and reducing strain on the engine. These aren’t just theoretical concepts, but critical practical skills to enhance your engine’s lifespan.
Balanced Air-to-Fuel Ratio and Monitoring
Having a balanced air-to-fuel ratio across all cylinders and employing an engine monitoring unit enhances the leaning process and provides invaluable feedback about your engine’s health.
The Journey of Mastery
Mastering these techniques requires practice, understanding, and time. Be patient and persistent, and these practices will become second nature, enabling you to operate your aircraft engine optimally.
To conclude, we hope that this post has illuminated the complexities of aircraft engine leaning. Apply these insights, and you can navigate beyond flawed practices of the past, operating your aircraft engine efficiently and effectively. Stay informed, stay atop!
About Quest Aeronautics
Quest Aeronautics is a state-certified engineering office for aviation, dedicated to shaping the future of general aviation by providing innovative and cost-effective solutions to enhance aircraft performance and operations. With a focus on CS/FAR-23 and experimental/amateur-built (E/A-B) aircraft, Quest Aeronautics provides a range of services including flight testing, aircraft operations and maintenance consulting, high-quality aviation products, and tailored support for E/A-B projects. Collaborating with industry-leading partners, Quest Aeronautics is committed to delivering unparalleled support and expertise to individuals and organisations in the general aviation market.
About Author
Sebastian, the founder of Quest Aeronautics, is a driven and enthusiastic individual with a passion for aviation. Before delving into aviation, he gained valuable experience as a chemical process engineer and laboratory technician. Sebastian holds a Master of Science in Engineering and a commercial pilot licence, with several fixed-wing aircraft ratings under his belt. He has also completed an introduction course for fixed-wing performance and flying qualities flight testing at the National Test Pilot School in Mojave, CA and is compliance verification engineer for flight.