Mastering Aircraft Engine Leaning – Introducing “The Red Fin” Concept and Considerations for Optimal Operation
In a previous blog post, we delved into the intricacies of aircraft engine leaning, advocating the benefits of lean-of-peak (LOP) operations. We discussed how a cleaner and gentler combustion can enhance engine longevity, reliability, and the overall cost-efficiency of flight operations.
A Quick Recap
Referencing a chart from Lycoming’s Operator’s Manual (see below), we made two key observations. Firstly, exhaust gas temperature (EGT) peaks at the stoichiometric ratio, whereas cylinder dead temperature (CHT) peaks around 30°F rich-of-peak (ROP). This point – where the highest internal cylinder pressure (ICP) is found – is often mistaken by pilots as the optimal setting for maximum economy. Secondly, the CHT’s slope is more pronounced on the lean side of peak than on the rich side. This indicates that a slight reduction in fuel can significantly lower CHT, as opposed to the larger increase in fuel required to achieve a similar reduction on the rich side of peak.
Note: Maximum CHT & ICP are observed 40°F – 50°F ROP.
There are few, if any, compelling reasons to operate ROP during cruise flight. While the airspeed difference between operating 100°F ROP and 50°F LOP is a mere 6.5%, the fuel consumption drops by an impressive 40%. Moreover, LOP operations are gentler on your engine and its components.
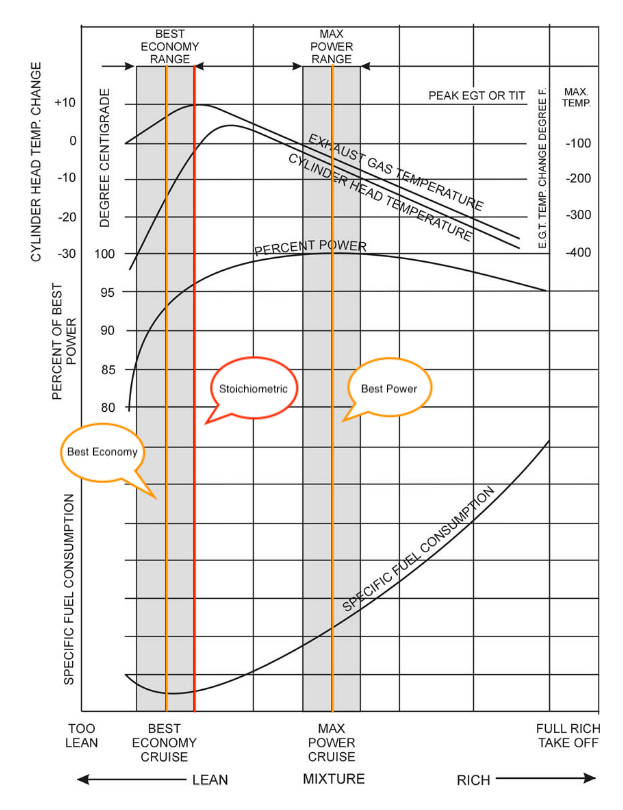
Avoid the Red Box
When it comes to engine operations, you have two primary choices: operate ROP for best power (75°F – 100°F ROP) or LOP for best economy (30°F – 70°F LOP). However, it is crucial to steer clear of the range between these settings, especially at higher power settings (above 70%). To emphasise this, we introduced the “Red Box” concept – an area to avoid at all times.
Using the same Lycoming chart, we illustrated the “Red Box” concept (see below). While we don’t have the specific engine power or absolute CHT values for this chart, we can still convey the intended message. Suppose the CHT change (indicated on the left side) is 420°F at 0° deviation; we aim to avoid any mixture settings that would push CHT above this temperature. The red box graphically represents this danger zone. For the depicted engine power, both rich (ROP) and lean (LOP) mixture settings are possible outside the “Red Box.”
For a more conservative approach, we use an orange box to denote a CHT limit of 400°F. This cautious stance indicates that while more fuel is necessary to maintain a lower CHT on the rich side of the peak, an even better economy can be achieved with less fuel on the lean side of peak. This demonstrates the efficiency of lean-of-peak operations, which not only protects the engine by managing temperatures but also conserves fuel.
Note: CHT is influenced by factors beyond ICP, including outside air temperature (OAT), the efficiency of the cooling system, airspeed, and air density, which correlates with density altitude.
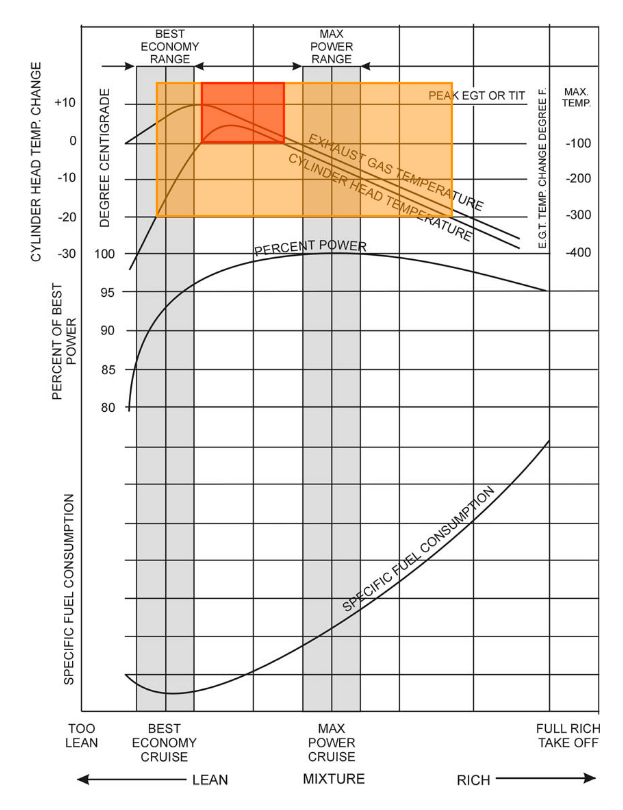
“The Red Fin” Concept
The “Red Box” is specific to certain engine power settings and varies by engine model. In addition, the “Red Box” expands with higher engine power and contracts with lower power. It vanishes below certain power levels (typically around 65 to 60% power), which is where the “Red Fin” concept becomes relevant. The “Red Fin” is an evolution of the “Red Box,” considering how the box’s size correlates with engine power. The diagram below depicts this relationship, highlighting the “Red Fin” as the zone to avoid.
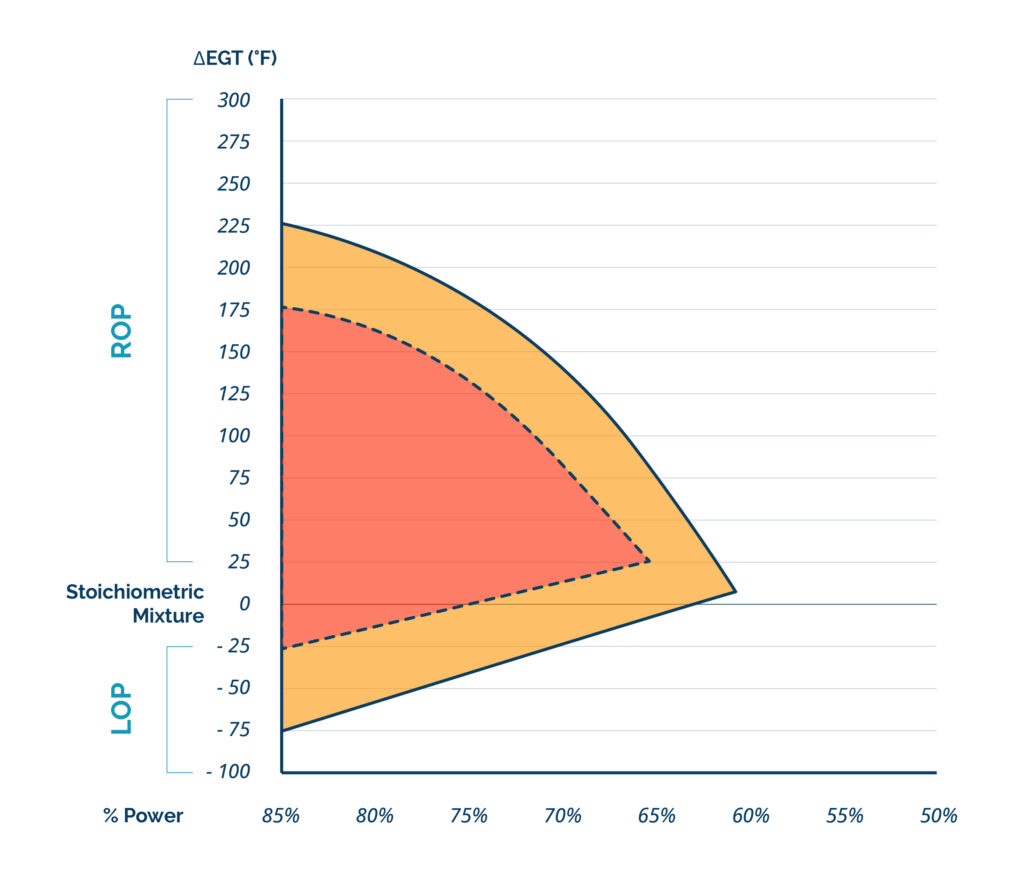
How to Fly the Fin
Optimal operating regions outside the “Red Fin,” shaded in orange and red, are recommended for most flights. Typically, experienced pilots will start their flight rich-of-peak, managing the mixture to stay clear of the “Red Fin” boundary. Upon reaching cruise altitude, a choice is made between power (ROP) for speed or fuel economy (LOP) for extended range.
Switching from ROP to LOP should be executed swiftly – by pulling the mixture quickly (within two to three seconds) to either reduce power or induce a slight engine roughness – to bypass the red zone. With experience in LOP operations at various altitudes, you can also lean directly to a known fuel flow setting.
Descent and approach are often conducted LOP, with mixture adjustments to avoid becoming too lean during altitude changes. Although running too lean at low power settings typically results in engine roughness, it serves as a reminder to enrichen the mixture. Crucially, for any missed approach or go-around, ensure the mixture is ROP to guarantee full engine power and maintain a safe distance from the “Red Fin” zone.
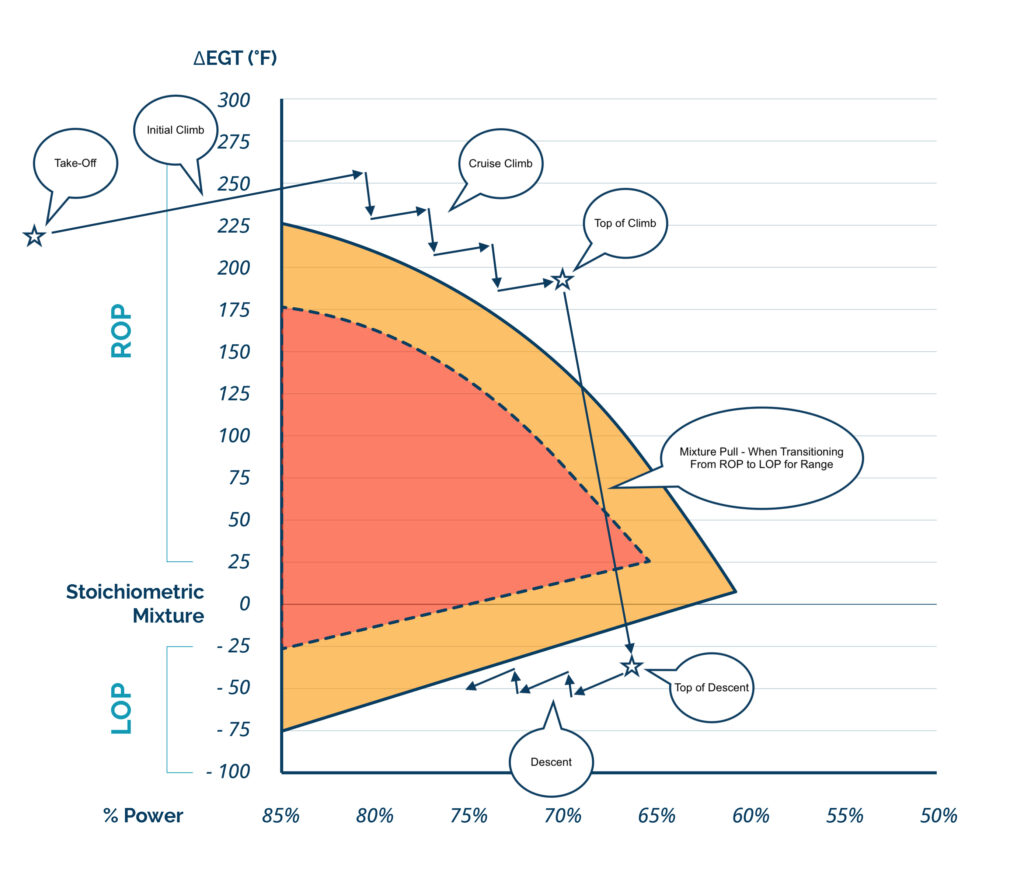
Naturally Aspirated vs. Turbocharged Engines
There’s a significant operational difference between naturally aspirated engines, engines with altitude-compensating systems, and turbocharged engines. Engines equipped with altitude-compensating systems and turbocharged engines are simpler to operate because they don’t require pilot adjustments for mixture changes with altitude changes. This is because the manifold pressure in turbocharged engines remains constant regardless of altitude, and altitude-compensating systems automatically adjust the mixture, keeping the air-to-fuel ratio stable.
Additional Operational Considerations
Many pilots are aware of the “backside of the power curve,” also known as the “region of reversed command.” In normal cruise flight, you pitch the aircraft to maintain altitude and adjust power to maintain airspeed. However, when operating on the backside of the power curve, your control inputs reverse. You pitch the aircraft to maintain airspeed and adjust power to control altitude. This requires a fundamentally different approach to aircraft control.
Similarly, though less commonly understood, is a concept that applies when operating ROP versus LOP. Generally, ROP is the domain of excess fuel, while LOP is the domain of excess air. When adjusting engine power, you must consider which reactant – air or fuel – is in shorter supply.
- For Rich-of-Peak Operations: Since this regime involves excess fuel, adjusting engine power requires modulating the throttle and/or propeller controls. This regulates the limiting factor – airflow – into the engine to achieve the desired power output.
- For Lean-of-Peak Operations: Here, with excess air, power adjustments are made by tuning the mixture control. This manages the limiting factor – fuel flow – to change the engine power as needed.
Conclusion
Mastering the art of aircraft engine leaning is an essential skill for the advanced pilot-owner. The introduction of the “Red Fin” concept provides a clear visual guide to optimise engine performance while safeguarding against the dangers of operating in the “Red Box” region. Whether navigating the power settings of naturally aspirated or turbocharged engines, understanding the nuances of rich-of-peak (ROP) and lean-of-peak (LOP) operations is crucial.
For ROP, remember that it’s the regime of excess fuel; hence, power is adjusted by managing airflow. Conversely, in the LOP regime, excess air dictates that fuel flow adjustments are key for power control.
This knowledge not only contributes to more efficient and economical flying but also to the longevity and reliability of your engine. Embrace these insights and carry them into every flight, ensuring that each decision made from the pilot’s seat is informed, precise, and beneficial to the health of your aircraft’s heart: its engine.
About Quest Aeronautics
Quest Aeronautics is a state-certified engineering office for aviation, dedicated to shaping the future of general aviation by providing innovative and cost-effective solutions to enhance aircraft performance and operations. With a focus on CS/FAR-23 and experimental/amateur-built (E/A-B) aircraft, Quest Aeronautics provides a range of services including flight testing, aircraft operations and maintenance consulting, high-quality aviation products, and tailored support for E/A-B projects. Collaborating with industry-leading partners, Quest Aeronautics is committed to delivering unparalleled support and expertise to individuals and organisations in the general aviation market.
About Author
Sebastian, the founder of Quest Aeronautics, is a driven and enthusiastic individual with a passion for aviation. Before delving into aviation, he gained valuable experience as a chemical process engineer and laboratory technician. Sebastian holds a Master of Science in Engineering and a commercial pilot licence, with several fixed-wing aircraft ratings under his belt. He has also completed an introduction course for fixed-wing performance and flying qualities flight testing at the National Test Pilot School in Mojave, CA and is compliance verification engineer for flight.