Protecting Your Aircraft Engine from Rapid Damage.
Detonation and pre-ignition are two distinct abnormal combustion events that can arise in internal combustion engines (ICEs). It’s essential to prevent these events to protect your aircraft engine. While they’re independent, they’re sometimes mistakenly used interchangeably. However, one can lead to the other; for instance, detonation can trigger pre-ignition. Both pose significant risks and have the potential to damage your aircraft engine swiftly.
Understanding Detonation
Detonation is a sudden combustion occurring near the peak pressure point during the combustion process. This combustion happens before the standard flame front reaches that specific point, primarily due to excessive pressure and temperature in the combustion chamber. The severity of detonation can range from mild to severe. In extreme cases, it can damage your aircraft engine’s spark plugs, pistons, and cylinders within minutes.
You can detect detonation through a distinct knocking sound, a result of erratic pressure pulses. On an engine monitor, this event is evident through a climb in cylinder head temperature (CHT) and a drop in exhaust gas temperature (EGT). Specialised engine test stands can measure these pressure pulses, showcasing them as sharp fluctuations in internal cylinder pressure (ICP), as visualised in the subsequent image.
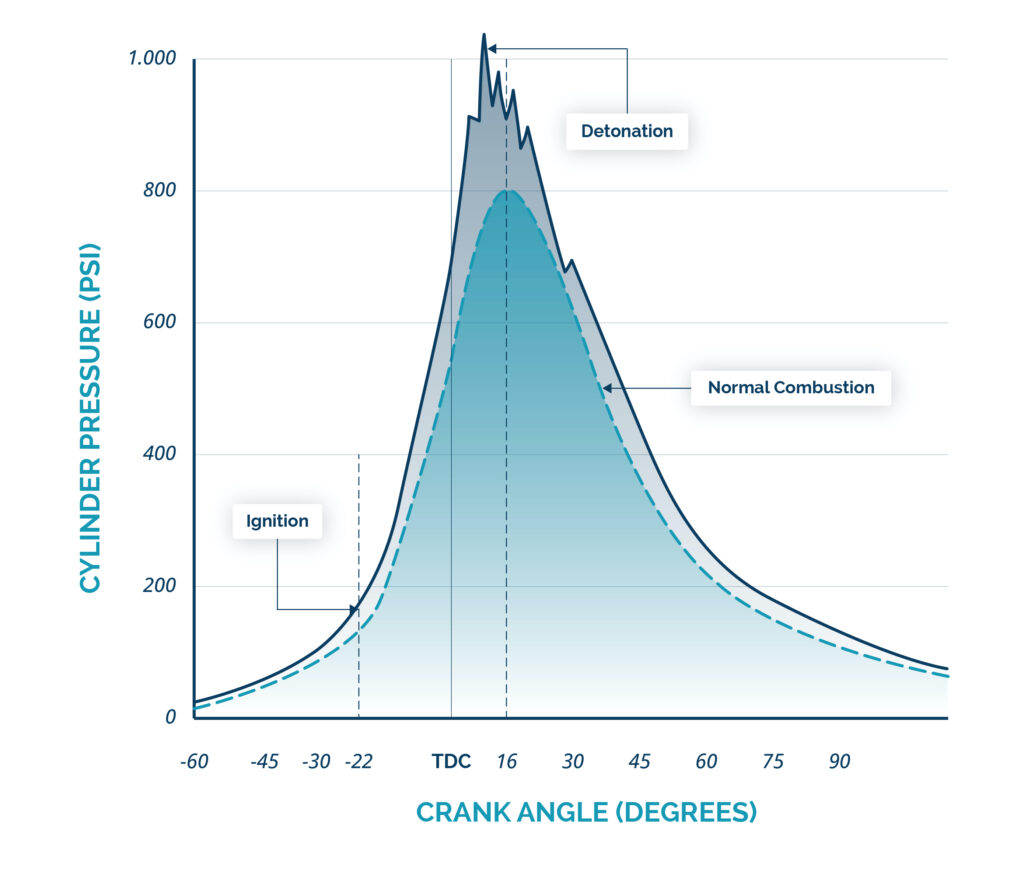
Pre-Ignition Explained
Pre-ignition occurs when the combustion mixture ignites before the spark plugs or ignition system sparked. This premature combustion imposes immense stress on the aircraft engine, as most of the combustion unfolds before the piston reaches its top-dead centre. Overheated spark plug tips, carbon or lead deposits in the combustion chamber, or occasionally, a burnt exhaust valve can serve as unintended ignition sources.
While detonation results in a sharp pressure spike near the peak pressure point over a short duration, pre-ignition generates intense, sustained pressure – potentially throughout the compression stroke. Pre-ignition, not only more destructive, is also elusive in detection. Often, its presence only becomes evident post significant engine damage. However, an increased CHT and erratic EGT can help detect pre-ignition.
Detonation Induced Pre-Ignition
Prolonged exposure to heavy detonation can raise temperatures and disturb the protective boundary layer, leading to overheating of spark plug electrodes and other combustion chamber components. Once these elements start to glow, they might trigger pre-ignition, culminating in rapid cylinder destruction. A subsequent teardown and analysis would display signs of both detonation and pre-ignition damage, but it’s the latter that delivers the fatal blow to the engine.
The Results of Detonation and Pre-Ignition
Detonation and pre-ignition can rapidly lead to catastrophic engine failure. These issues can cause fractured spark plugs (both electrodes and insulators), broken piston rings and lands, typical pitting on the piston crown, and heat-related damages like piston skirt scuffing and melting in the crown-to-land area.
If a piston crown appears sandblasted or a ring land shows fractures, heavy detonation likely caused it. A melted hole in the piston crown’s centre typically indicates pre-ignition. Other pre-ignition signs include spark plugs with melted electrodes or insulators splattered with molten metal.
How to Avoid Detonation and Pre-Ignition
Two main factors play a role in averting detonation and pre-ignition: the installation and operation of an aircraft engine. These aspects often intertwine.
Installation
Optimising the engine installation and its surroundings is a crucial first step to counteract detonation and pre-ignition. Various design and installation components must be scrutinised for smooth operation.
Design & Installation
A solid propulsion system design and installation lay the foundation for a hassle-free flying experience. It’s crucial to adhere to the engine manufacturer’s guidelines and constraints. Notable areas include the design and specifications of the induction and exhaust systems. Any deviations from the provided design (in terms of geometry, material, etc.) or limits (such as pressure and flow rate) might induce abnormal combustion events.
Always ensure that every engine control interface is accurately installed and adjusted to prevent unintended inputs.
Ignition System
Maintaining the ignition system is paramount. Specifically, correct ignition timing is crucial. Overly advanced ignition timing can result in elevated CHT temperatures. Moreover, damaged spark plugs, especially their ceramic insulation, can hamper the system’s performance.
Fuel System
Ensuring and fine-tuning the fuel system for optimal operation is vital. A poorly adjusted fuel system might cause the engine or individual cylinders to run too lean, narrowing the margins against detonation.
Watch for partially clogged fuel injector nozzles, evident by higher CHTs. Such blockages often appear after fuel system maintenance. Regularly conduct in-flight test procedures to ensure your fuel, ignition, and induction systems are in top condition.
During take-off, it’s essential to monitor and adjust fuel flow, especially when using PMA replacement cylinders with enhanced volumetric efficiency or aftermarket intercoolers for turbocharged engines. The full-power fuel flow indicated on your OEM fuel flow gauge might be insufficient to maintain the CHT within safe levels.
Cooling
To stave off high cylinder temperatures, it’s essential to properly set up and maintain the cooling system. Regularly inspect internal cylinder baffles, flexible seals, cowl flaps, and other components of your aircraft engine’s cooling system. Keeping them in peak condition guarantees effective engine cooling.
Operation
Once you’ve confirmed the correct installation, the next focus is aircraft operation. Several essential factors come into play here.
Engine Control - MAP/RPM/Mixture
Engine control significantly influences not just the peak ICP but also its timing in relation to the crankshaft angle. When manifold pressure (MAP) drops, the peak ICP decreases and shifts later (in terms of crank angle). The opposite is true for propeller RPM. As for the mixture control, it affects ICP differently based on whether the fuel flow is reduced on the lean- or rich-side-of-peak EGT. Peak ICP increases and moves forward when rich-of-peak (ROP) and decreases and shifts later when lean-of-peak (LOP). The relationships are depicted in the three figures below.
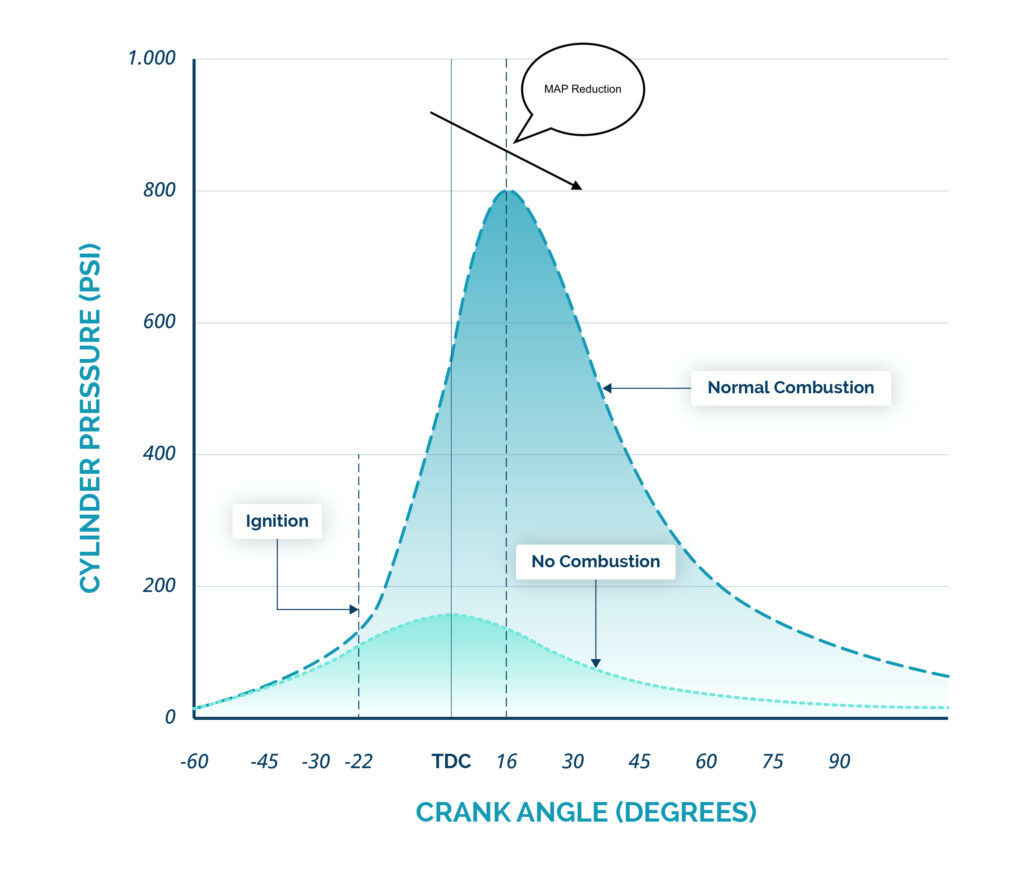
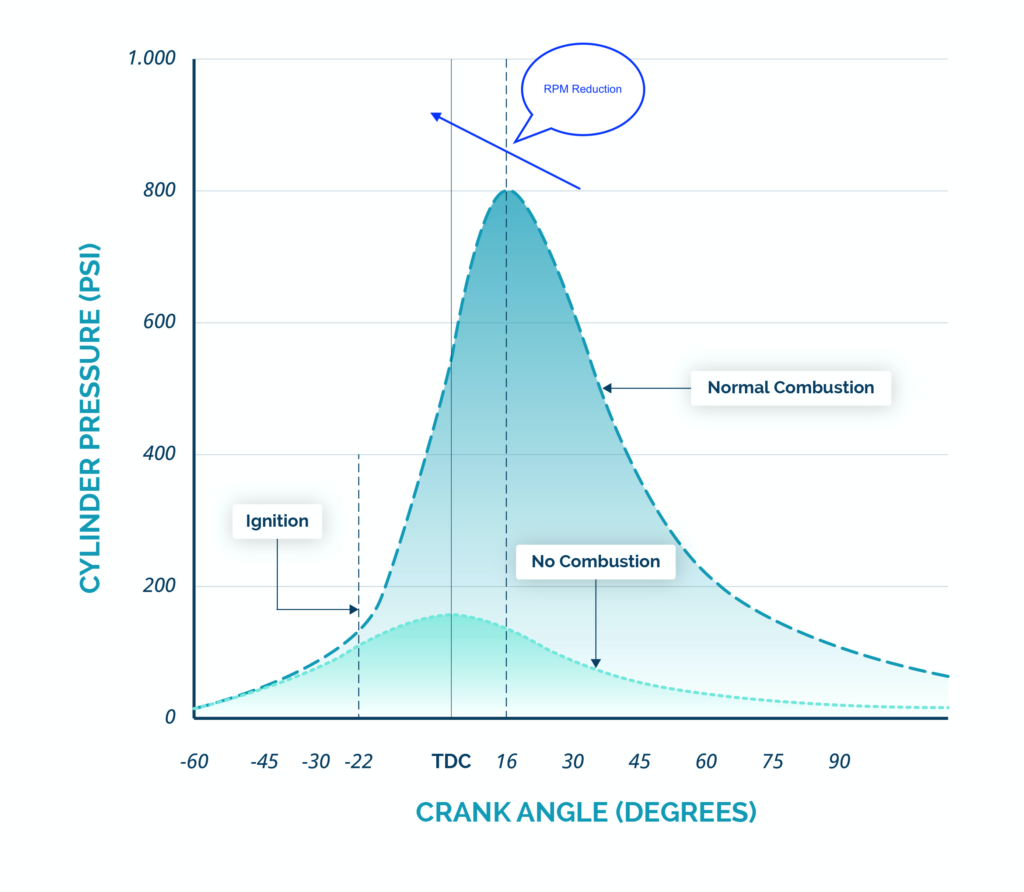
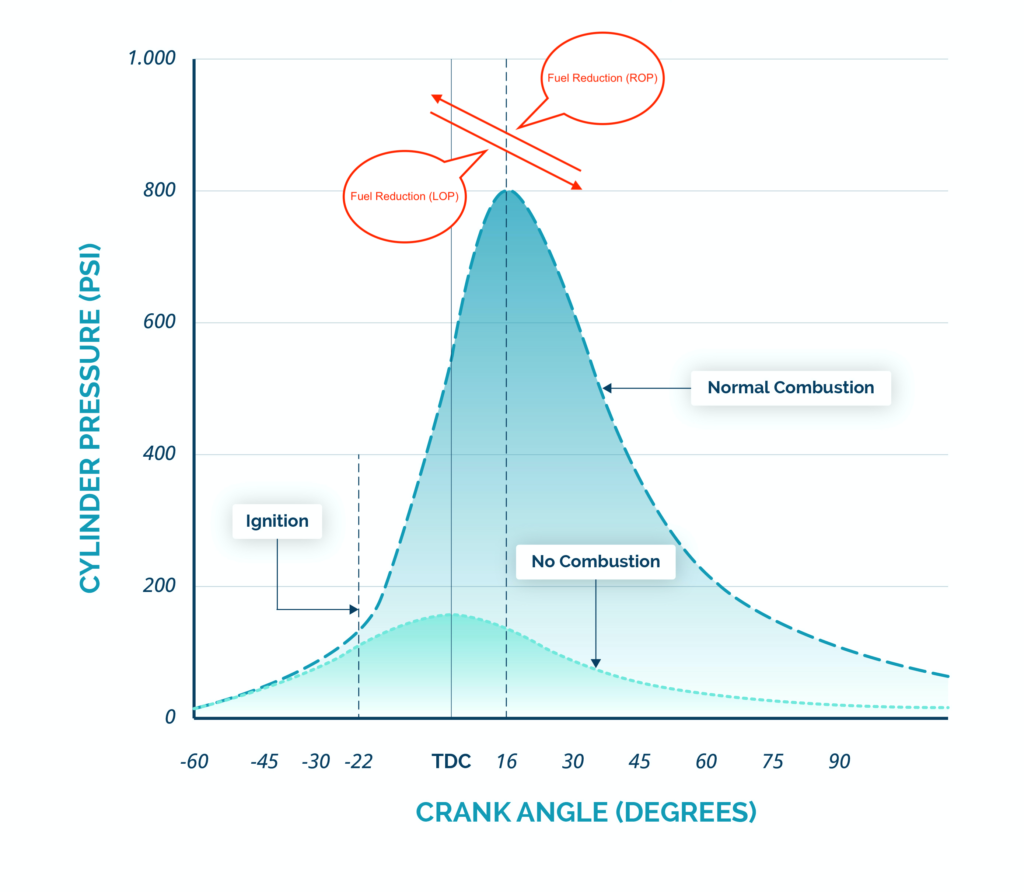
Fuel Quality
High-quality fuel stands as one of the best defences against detonation. Always use fuel approved by the engine manufacturer. But there’s more to consider. Beyond the octane number, be aware of seasonal variations. For instance, in certain regions, summer and winter-specific fuels are available. Cold-climate fuels contain additives to enhance spray atomisation and ignition. However, these can reduce the detonation margin and increase the risk of vapour locks in hot climates.
Over-Square Operation - Within Limits
We advocate for over-square operation during cruise. This means the propeller speed (divided by 100) is lower than the manifold pressure in InHg. Over-square operation is crucial, especially for LOP operation of Continental and Lycoming aircraft engines. Nevertheless, always heed any limitations set by the engine manufacturer, available in the operators’ manuals.
Carburettor Heat
Carburettor heat prevents ice accumulation in carbureted aircraft engines. Various methods achieve this, with the prevalent one routing outside air via hot engine parts like mufflers to the carburettor’s air inlet. While effective, incorrect use or poorly adjusted systems can lead to excessively high induction air temperatures and combustion abnormalities.
Temperature Limits
Always respect temperature limits, especially concerning cylinder head and induction air. Adjust your aircraft engine operations, and if available, utilise engine controls and cowl flaps to remain within set boundaries. Ensure both your fuel and cooling systems function optimally.
Keeping it Clean
Minimise ground operation and lean the aircraft engine aggressively while on the ground. Properly leaning your engine and maintaining optimal cylinder head temperatures in flight reduces the accumulation of carbon and lead deposits. This practice lowers the risk of deposits potentially causing pre-ignition. For more on engine leaning, refer to our dedicated blog post on the subject.
Conclusion
Detonation and pre-ignition can pose serious threats to the safety and longevity of an aircraft engine. But with a comprehensive understanding of their causes, proactive installation practices, and diligent operational strategies, these risks can be significantly mitigated. As aircraft owners, pilots, or maintenance personnel, it’s crucial to be well-versed in both the theory and the practical aspects of engine care. By adhering to manufacturers’ guidelines, prioritising high-quality fuel, and consistently monitoring engine performance metrics, we can ensure not only smoother flights but also a longer, safer life for our engines.
The journey to mastering aircraft engine health is ongoing, and we aim to support and inform every step of the way. Fly safe and stay informed!
About Quest Aeronautics
Quest Aeronautics is a state-certified engineering office for aviation, dedicated to shaping the future of general aviation by providing innovative and cost-effective solutions to enhance aircraft performance and operations. With a focus on CS/FAR-23 and experimental/amateur-built (E/A-B) aircraft, Quest Aeronautics provides a range of services including flight testing, aircraft operations and maintenance consulting, high-quality aviation products, and tailored support for E/A-B projects. Collaborating with industry-leading partners, Quest Aeronautics is committed to delivering unparalleled support and expertise to individuals and organisations in the general aviation market.
About Author
Sebastian, the founder of Quest Aeronautics, is a driven and enthusiastic individual with a passion for aviation. Before delving into aviation, he gained valuable experience as a chemical process engineer and laboratory technician. Sebastian holds a Master of Science in Engineering and a commercial pilot licence, with several fixed-wing aircraft ratings under his belt. He has also completed an introduction course for fixed-wing performance and flying qualities flight testing at the National Test Pilot School in Mojave, CA and is compliance verification engineer for flight.