Why In-Flight Test Procedures Matter.
In-flight test procedures are among the first things we ask clients to perform when we start working together or when they acquire a new (to them) aircraft. These tests quickly establish a baseline for your engine’s health.
Completing the following in-flight test procedures takes about an hour. Yet, it provides valuable insights into your engine’s performance. It can uncover issues your maintenance shop or mechanic might miss or even fail to understand. This process lays the foundation for competent and safe aircraft operation.
Recently, we carried out these in-flight tests on a Diamond DA40 with a Lycoming IO-360-M1A. The results revealed issues no one had previously identified. Some tests will need repeating after recommended fixes are implemented.
We perform these tests to check three critical areas:
- Mixture distribution among all cylinders (essential for lean-of-peak operation),
- Ignition system health, and
- Induction system integrity.
The data you gather will guide your decisions on maintenance and engine operation.
How We Conduct the In-Flight Tests
First, we establish the aircraft at 7000 ft pressure altitude and set 65% power. We begin with the mixture distribution test, completing three mixture sweeps: from 100°F ROP to LOP (onset of roughness) back to 100°F ROP. We stop halfway through the third sweep.
Next, while still at the same altitude and power setting, we perform the ignition stress test (magneto check) in lean-of-peak conditions. Finally, we enrich the mixture to full rich, descend to 5000 ft pressure altitude, and execute the induction leak test at two MAP points.
The DA40’s Garmin G1000 system makes it easy to record all flight and engine data. By inserting an SD card into the top MFD slot, we capture engine parameters with a 1-second sample rate.
Pre-Flight Briefing for In-Flight Test Procedures
Before performing these procedures, we brief our clients thoroughly. Although the procedures are not difficult, a complete briefing ensures safety and accuracy. We always recommend using a safety pilot.
We’ve explained these procedures in detail in our dedicated blog post here: In-Flight Test Procedures Guide. You can download a free description and test cards at the end of that post.
Mixture Distribution Test
For naturally aspirated engines like the IO-360-M1A, the mixture distribution test is performed with wide-open throttle (WOT). We set propeller speed to 2200 RPM and achieved 23.25 InHg manifold pressure. Ideally, we start the first sweep at 100°F ROP, but in this case, we began full rich due to unknown to us aircraft.
We noted difficulties setting the mixture precisely, and the fuel flow gauge showed erratic readings. This prevented a smooth sweep. The data showed a GAMI spread ranging between 0.3 and 1.1 GPH.
The EGT from cylinder 2 dropped sharply while cylinder 1’s EGT rose on that occasions indicating a high GAMI spread. These irregularities indicate the data is inconclusive. The test must be repeated after checking the fuel system and fuel flow gauge. The lean range was also at the high limit (>300°F).
Note: The DA40 uses a control quadrant instead of a Vernier control, making fine adjustments harder. This contrasts with Cessna singles, which use push/pull or Vernier controls for precise mixture management.
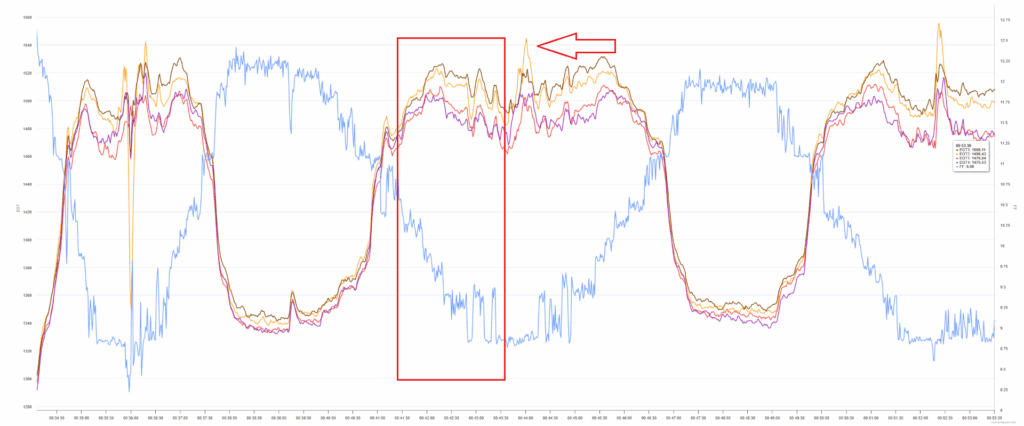
Cylinder | Fuel Flow (GPH) | GAMI Spread | Lean Range (°F) |
---|---|---|---|
EGT4 | 10.1 | 0.3 – 1.1 | 305 |
EGT3 | 9.9 | 315 | |
EGT1 | 9.8 | 295 | |
EGT2 | 8.9 | 320 | |
Ignition Stress Test
We performed the ignition stress test halfway through the third mixture sweep, with the engine aggressively leaned. We maintained the same power setting and altitude, conducting a magneto check: both – left – both – right – both.
We typically collect data for at least 10 samples times the engine monitor’s sample rate but no less than 30 seconds overall.
The graph and table below show that EGTs increased more with only the right magneto operating. This difference suggests possible variations in ignition timing, which should be set identically at 25° BTDC for this engine. Cylinder 1 showed a different EGT rise but remained stable, suggesting no active ignition fault.
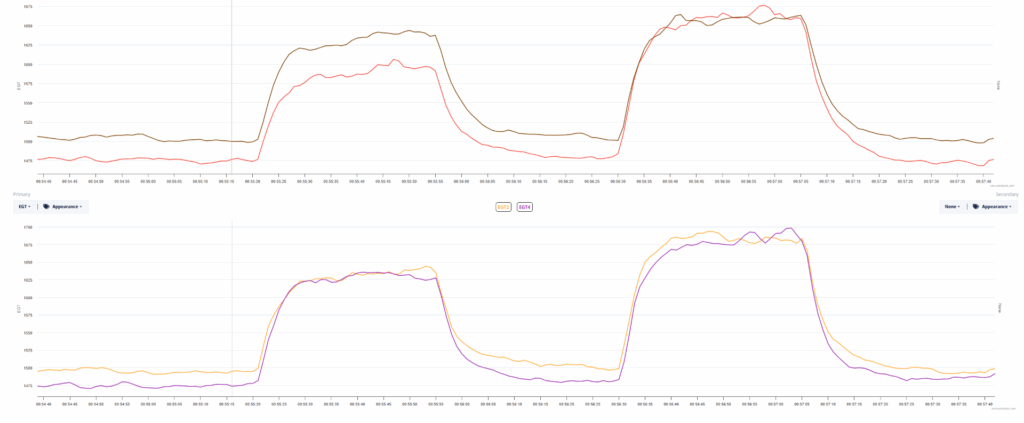
Parameter | Both | Left | Both | Right | Both | Delta Left | Delta Right | Remarks |
---|---|---|---|---|---|---|---|---|
EGT1 | 1475 | 1595 | 1480 | 1660 | 1475 | 120 | 185 | Right-mag EGT rise suggests different ignition timing. |
EGT2 | 1495 | 1635 | 1505 | 1680 | 1495 | 135 | 185 | |
EGT3 | 1500 | 1640 | 1510 | 1660 | 1500 | 135 | 160 | |
EGT4 | 1475 | 1635 | 1480 | 1675 | 1485 | 160 | 195 |
Why EGT Rises During Single Magneto Operation
During single magneto operation, EGTs increase because the combustion process takes longer. With only one spark plug firing per cylinder, the flame front travels more slowly. This delay leads to incomplete combustion and more unburned fuel reaching the exhaust, causing higher EGT readings.
Induction Leak Test
To perform the induction leak test, we descended to 5000 ft pressure altitude, set WOT, and adjusted propeller speed to 2400 RPM. We maintained this configuration for 30 seconds. Then, we reduced MAP by 10 InHg and stabilized for another 30 seconds.
A larger EGT rise during the low MAP phase indicates a tight induction system. Conversely, a smaller EGT increase suggests an induction leak in the respective cylinder or pair. Our data showed cylinders 1 and 3 had a smaller EGT delta than cylinders 2 and 4, pointing to a potential induction leak in the 1/3 pair.
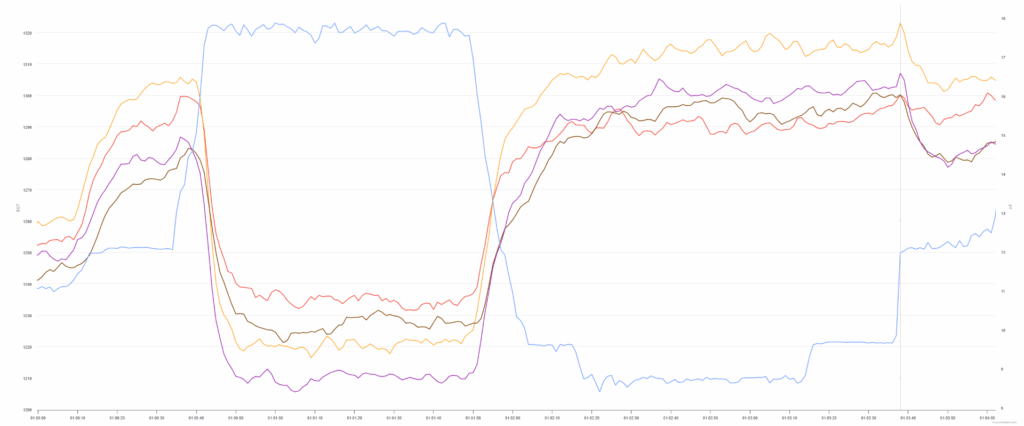
Parameter | High MAP | Low MAP | Delta | Remarks |
---|---|---|---|---|
EGT1 | 1237 | 1290 | 53 | Smaller delta may indicate induction leak on cyl. 1 & 3 |
EGT3 | 1225 | 1292 | 67 | Smaller delta may indicate induction leak on cyl. 1 & 3 |
EGT2 | 1220 | 1317 | 97 | |
EGT4 | 1211 | 1301 | 90 | |
MAP | 25.1 | 15.0 | -10.1 |
Conclusion
Performing in-flight test procedures is a powerful tool for evaluating your engine’s health. It helps you make data-driven decisions, reduce operating costs, and improve safety. Repeating these tests after repairs ensures your aircraft performs at its best.
About Quest Aeronautics
Quest Aeronautics is a state-certified engineering office for aviation, dedicated to shaping the future of general aviation by providing innovative and cost-effective solutions to enhance aircraft performance and operations. With a focus on CS/FAR-23 and experimental/amateur-built (E/A-B) aircraft, Quest Aeronautics provides a range of services including flight testing, aircraft operations and maintenance consulting, high-quality aviation products, and tailored support for E/A-B projects. Collaborating with industry-leading partners, Quest Aeronautics is committed to delivering unparalleled support and expertise to individuals and organisations in the general aviation market.
About Author
Sebastian, the founder of Quest Aeronautics, is a driven and enthusiastic individual with a passion for aviation. Before delving into aviation, he gained valuable experience as a chemical process engineer and laboratory technician. Sebastian holds a Master of Science in Engineering and a commercial pilot licence, with several fixed-wing aircraft ratings under his belt. He has also completed an introduction course for fixed-wing performance and flying qualities flight testing at the National Test Pilot School in Mojave, CA and is compliance verification engineer for flight.